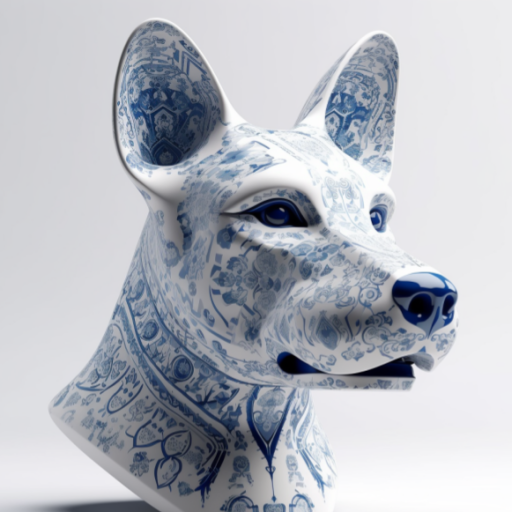
Christopher - Unmake Plastic
Designing a large billet compression mold- 20"x14"x8"/50.8cmX35.56cmX20.32cm, receiving about 92.59 lbs/42.49 kilos of shred. The mold will be filled, heated in a convection oven, the compression lid affixed, 6 large perimeter screws delivering clamping force through compressed springs, then retorqued at intervals until annealing.
I wonder about the needed clamping force. A Sheet Press employs an 8-tonn jack- which, in addition to clamping force, is tasked with raising the entire heating bed, mold, and plastic shred. The compressed area of the sheet press is ~10,000 sq cm, volume 20,000 cubic cm (for a 2 cm thick sheet), & 22 kilos; by contrast, the proposed mold features a compressed area of 2,090.98 sq cm, volume 42,487.656 sq cm, and weight of 42.49 kilos. What is the more critical aspect for determining clamping force needs- area, or volume?
With a sheet press, the mold is overfilled, then the jack is progressively applied until the upper press meets the mold top- pressure, in part, depends on the viscosity of the plastic! When designing the billet mold's compression lid, I'm inclined to build it as a stepped plunger, rather than a flat plate, to allow space in the mold for the shred, & to retain pressure; the alternative would be shred melted to fill the mold before compression, then overfilled & flat compression lid applied- the concern there being that most of the pressure would bleed out the side before acting to purge deep air bubbles. Thoughts?
Lastly, many small compression molds are just single-layer female and male shells, while brick injection molds are replete with ribs all around. All things considered, I'm inclined to rib-reinforce this monstrous molds; that said, due to commonly available stock dimensions, the billet mold will likely be fabricated from .635 mm (1/4") mild steel, for a combined billet/mold weight of near 90 kg!!! I'd love someone to give me cause not to add the rib weight!!